In this article, I’m going to give you my thoughts on the importance of infill and try and see what is the best 3D print infill pattern. I’m going to keep things simple for this one and as such some of the things I’m mentioning may seem basic to you. I think though that its good to sometimes go back to basics and there will also be some of you that are completely new to this.
So, what is the 3D print best infill pattern? The first thing to look at is patterns.
Choosing the Infill Percentages in 3d printing
If you look at a 3D printed model, you may be forgiven for thinking that it’s either completely solid or indeed hollow. If we’re talking about resin 3D printing then yes, it would be solid but in the world of FDM (Fused Deposition Modelling) 3D printing, the answer lies somewhere between the two.
I’m talking here about infill and it’s a crucial factor to bear in mind when printing a 3D model. The infill is basically the skeleton of your model and as such supports the materials by which its surrounded. Getting the right shape and size for the skeleton or infill is therefore essential to the structural integrity of your 3D print. But how do you go about deciding what the best percentages are for your infill and how does this actually affect your model?
Let’s take a closer look at what’s need to get the right infill balance.
What does infill mean in 3d printing?
We’ve referred to skeletons but let’s move away from that and get down to the bones of the subject (darn it!). So, let’s talk about what infill actually means in terms of 3D printing.
As you’re probably aware, FDM printing is done in layers and builds gradually from the base upwards. The outer part or wall of your model is the bit that you’ll see but this needs to have something to bond with to keep it intact. The wall is therefore printed as the thickest, solid part of each layer with the infill being made up of a framework of lines within the walls. This needs to be set as a percentage in order for the printer to know how much infill to print.
In order to set this percentage, you’ll need to set the parameters of your print in a slicing program such as Cura. As I said at the start of this piece, I may be preaching to the converted but Cura is the go-to slicer for the majority of 3D printing enthusiasts.
Cura will allow you to set and adjust multiple factors of your 3D model before you “slice” it and make it 3D printable. Setting the infill percentage is fairly straightforward in Cura and is literally a case of entering the percentage you want into the appropriate box.
I created this Star Wars related bookend a while ago which is pretty square so might not necessarily need a complex infill pattern. My default infill is a grid so in the images below from my Cura desktop, you’ll see the model as it is from the outside and then an “x-ray” view with a 10% infill then 20%. You’ll see the difference in just that small incremental increase.
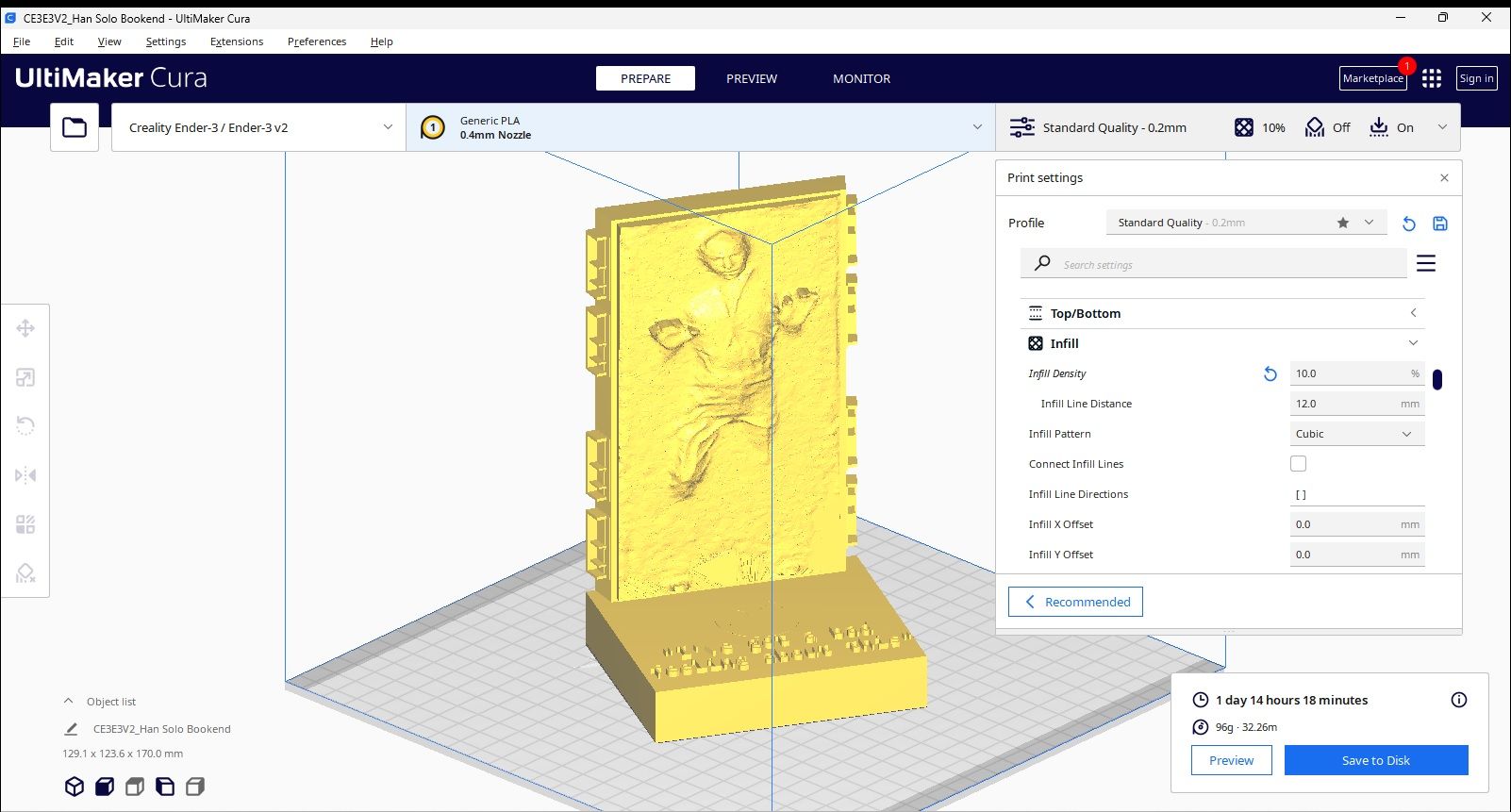
The model as it appears from the outside
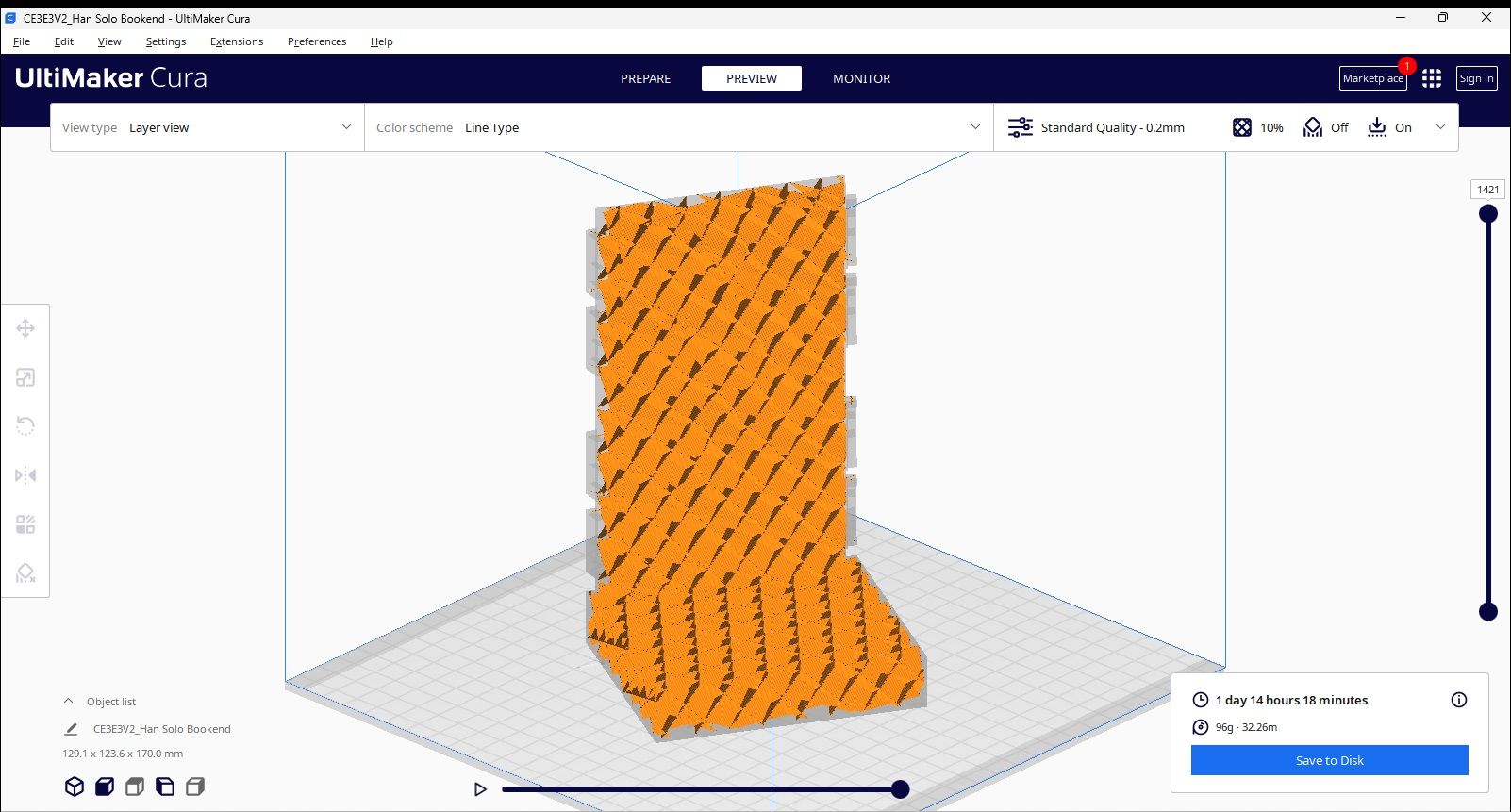
The interior of the model with a 10% infill grid pattern
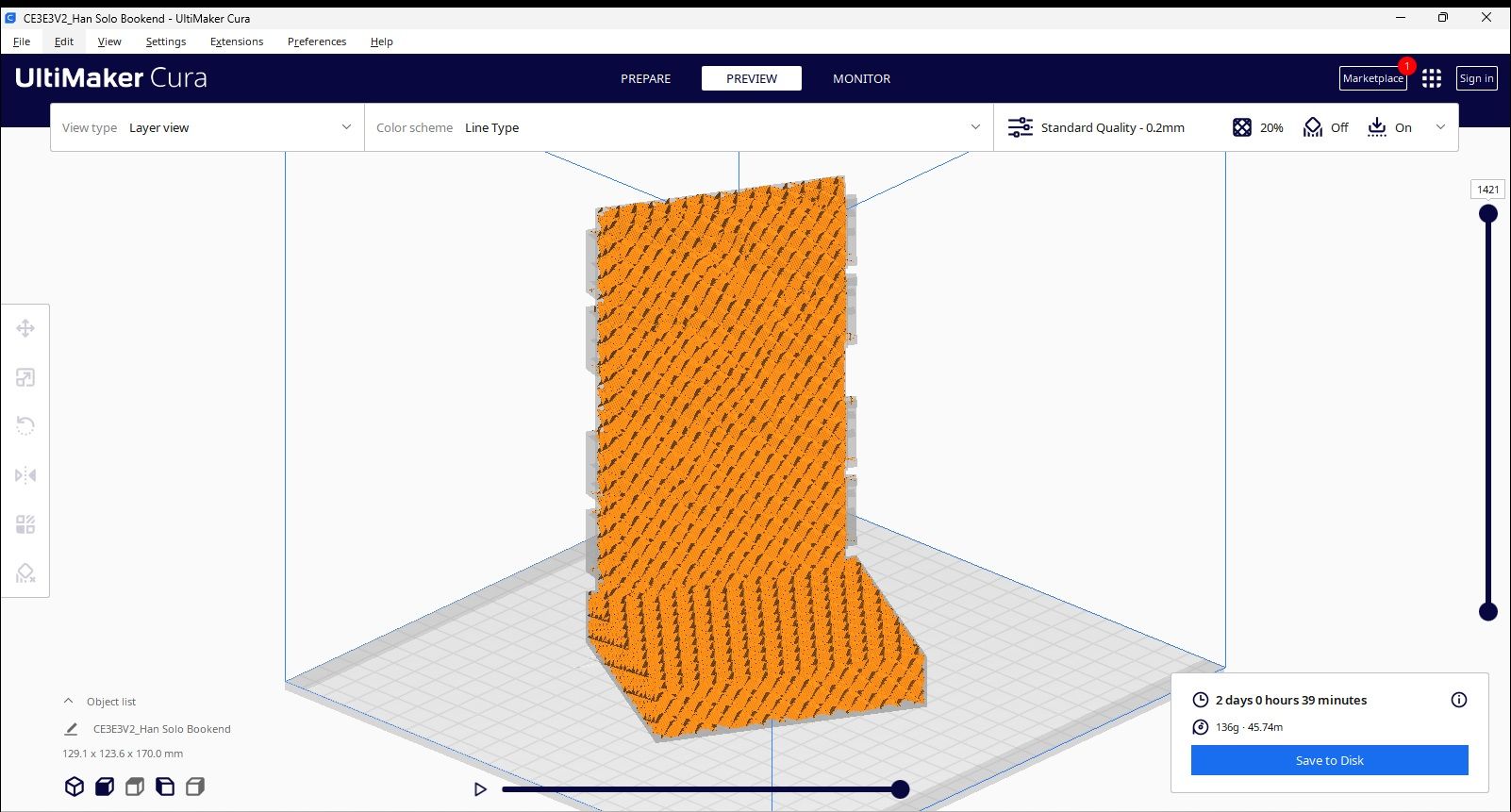
The interior of the model with a 20% infill grid pattern
I mentioned there that I tend to use a grid pattern for my infill but this can vary between different types of models. This might not seem that important but it can mean the difference in success or failure of your print. For instance, choosing a “zig-zag” infill may ultimately provide less internal support than a “grid” or “honeycomb” pattern. This will depend on the model itself and whether there are thicker top layers to your print which might need that extra support.
But again I ask, what percentage do you decide upon? Let’s take a look at that and another couple of model examples using different infill patterns and percentages.
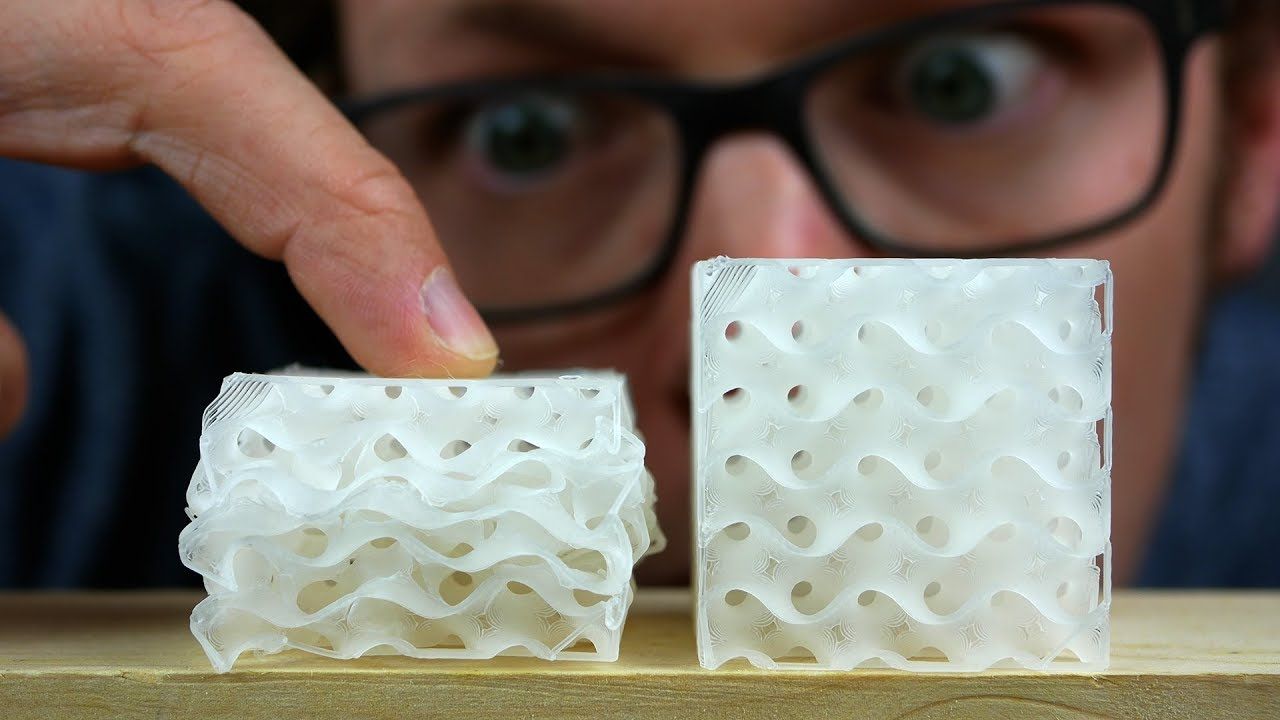
3d printing infill percentage
As I’ve discussed, the infill percentage that you set for your model will determine its structural integrity and stability. However, there are other factors to consider in terms of material usage and print time. A high percentage of infill will naturally use more filament and will definitely increase the time it takes to complete your print.
The main thing we’re looking at here though is what sort of printed items need what percentage of infill. Let’s have a look at this in the table below.
Percentage Infill |
Type of 3D printed item |
Description |
0-20% |
Non-functioning parts |
Items such as display models or figurines. Minimal infill
is needed unless some aspects need more supports as mentioned previously |
20-40% |
Light use |
These would be functional parts such as gear wheels in working
models or children’s toys etc. |
40-100% |
Heavy duty |
Items that need to withstand greater force such as small
tools or parts for electrical machinery |
It’s worth noting that adding an in fill above 60% percent won’t necessarily continue to increase the strength of your printed item as its tensile strength will still be a factor. Another thing to note is the use of different filament types which also have different strengths and weaknesses. This leads us onto the next consideration which is…
Infill Percentage vs Strength
Increasing the percentage of your infill isn’t necessarily a guarantee of increased strength. You’ll need to consider the shape or geometry of your model as well as its orientation when printing. A model of a human figure for example may have extended limbs which are supported during printing but won’t be when those supports are removed. The strength of those limbs on your model may then need extra reinforcement from a higher infill percentage if they’re going to stay in situ.
Looking back then at our refence table above, our example of a model figure would require an infill of between 0 and 20%. An infill of 0% just won’t work so it would need to be a minimum of 10% but, given the extended limbs scenario, you’d be better off with 20%. This will give overall structural support and ensure that the weaker parts of the model stay intact.
As I’ve alluded to, different filament types will also play a part in deciding the appropriate infill percentage for your model. For example PLA is the most commonly used type of filament in 3D printing due to its versatility and lower working temperatures. However, it’s not the strongest of materials so even using it for models with a higher percentage infill may still show its weaknesses. Probably the second most commonly used filament is ABS which has a higher working temperature but displays greater strength than PLA. When using ABS you may find that, using our model figure again, you can maintain a 10% infill and still get the strength you need in the limbs.
I’ve also mentioned the fact that increasing infill over 60% may not in fact be worth it in terms of hoping for extra strength. We’ll use a different example for this and look at an everyday item such as a plastic rule which you might have sitting on your desk. If you’ve purchased this from your local stationary store it will undoubtedly have 100% infill as it won’t have been 3D printed but more likely injection molded. It may still have some flexibility to it but I’m sure if you bend it enough it will reach a breaking point at some stage. This would be the same if you’d 3D printed the rule with 60%+ infill, the breaking point may be further round the bend but it will still break at some point. By the way, please don’t deliberately break your plastic rule, just take my word for it!
More Models
So, I’ve shown you what a fairly standard model shape that needs no real strength looks like in terms of 3D print best infill pattern and percentages. Let’s now look at another couple of examples which will give you an indication of what you might need for more complex designs.
Both of these designs and their files can be found in my other article, “Decoding the Mystery: How Much Filament Does a 3D Print Really Use?” which will also give you a good idea as to how much filament you might be using.
The first of these more complex models is one of the One Piece character, Monkey D. Luffy and shows what I mean by different parts maybe needing different infill percentages and patterns. The model itself is divided into six individual printed parts so in this case, it’s a bit easier to change the infill parameters for each part.
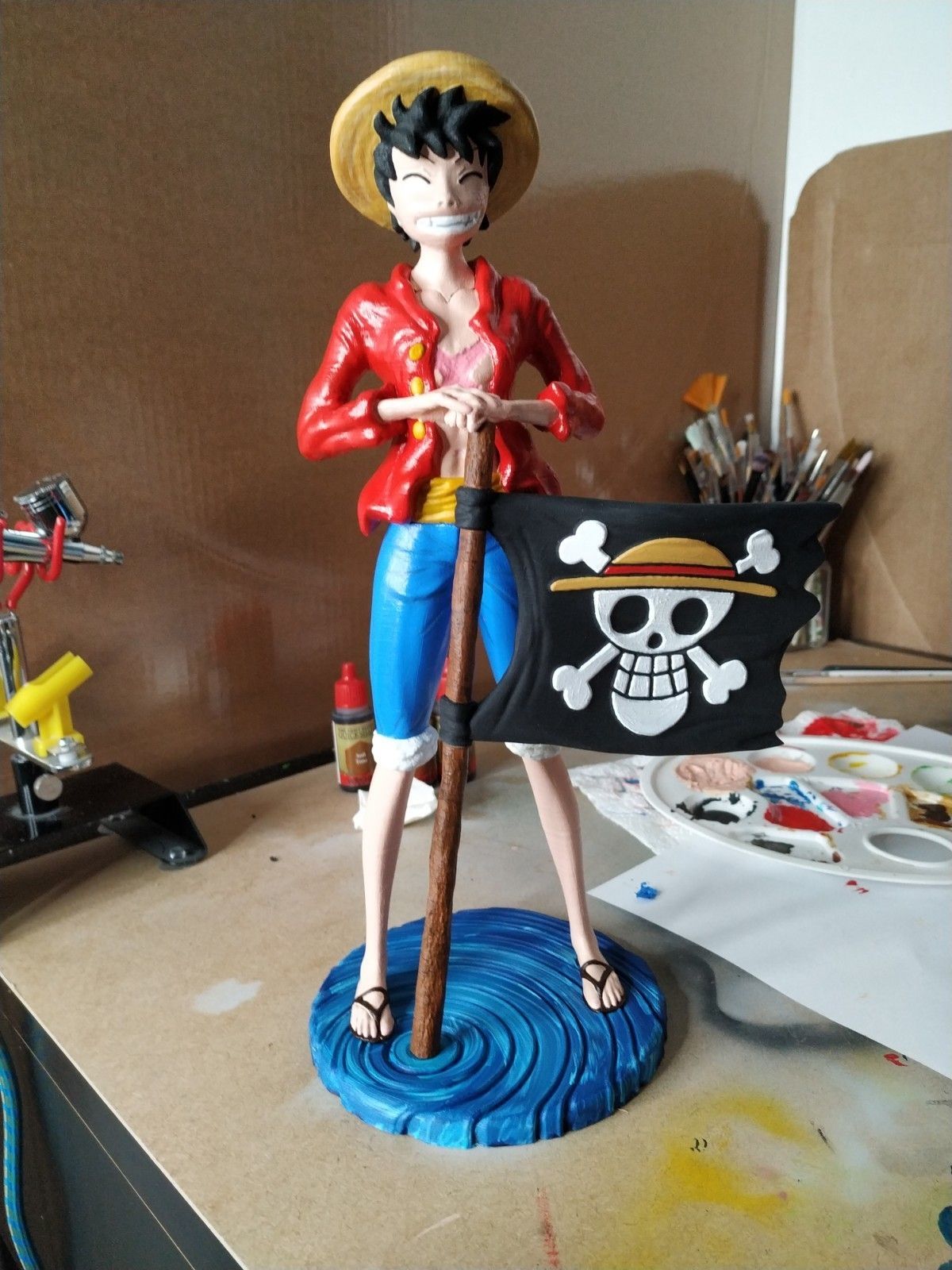
For instance, the base is fairly uniform and sturdy so I’d go for a 10-15% grid patten infill. The legs and the flag have some thinner parts and will therefore need a bit more strength from the infill. For these parts I’d suggest at least a 20% infill but for a bit more rigidity, you could even go for 25-30%.
With the jeans, head and torso you have a bit of a dilemma as the main part of the pieces are solid but with the hat brim for instance, there’s potential for breakage or weakness. Therefore, I’d err on the side of caution and go for a similar infill percentage as the legs and flag, so 20-30%.
As for patterns, the strongest patterns are those that tesselate well so squares and hexagons really. As I said earlier, using a zigzag or one of the other non-tessellating patterns may make the thinner parts a bit weaker.
If you want to have a go at printing this model yourself then take a look at the free download on Cults 3D.
The next model I’m going to show you is another that I’ve looked at before but this time we have a larger scale involved and at least one part that needs some protective infill.

Saitama, or One Punch Man, is the eponymous hero of the extremely popular Manga and Anime series. This model may look fairly standard as it is just of the character in a standing pose but have a look at his cape. That will need both a strong infill and decent support structure. At the moment though we’re only concerned with the infill so again, it’s a case of considering carefully what you’ll need.
The main thing with infill over lager models is firstly to ensure that the infill is sufficient to provide that internal support that I mentioned. Using a 10% infill on a model such as this one will leave the thinner, longer parts such as the legs with little structure so will be prone to breakage and collapse. This would possibly be both during and after printing.
The next thing to consider, as with all models really, is the integrity of what could be the weakest part of the model. In the case of the Saitama, we go back to the legs but also to the aforementioned cape. The best thing to do in this case then is to account for any weak spot and use an infill of 20-30%. Again, I’d go for a grid or honeycomb pattern infill for this sort of model.
If you want to try your hand at printing this model then you can download it for free from CG Trader.
Now, you may be thinking that this doesn’t marry up with the table above but I am erring on the side of caution here and going by my own experiences of 3D printing over the years. The table is a good starting point guide but trial and error will maybe blur the lines between each percentage range.
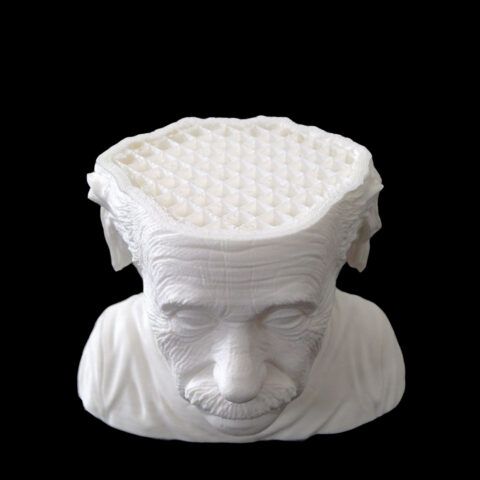
Final thoughts
So, I’ve looked at the different infill percentages that might work best for certain types of 3D prints and hopefully this has given you some idea as to the best strategy for you. Some of this may however come down to a trial-and-error scenario so don’t be disheartened if your print doesn’t work perfectly with what you’d expect to be the correct infill. As I’ve said, there are different variables that may affect the strength of your model and in turn, slight adjustments to the infill percentage may be needed.
In short then, try to use these as a guide and remember to bend but don’t break the rules!
Member discussion